It always pays to look again when it comes to stealing ideas. While I saw them the first time, it just dawned on my how you're using receivers for various extensions. While this isn't a new idea, your use of them is. I'd like to incorporate some in my new design, but what they get for those little rascals is ridiculous for my budget.
Still, I'm going to file your ideas away and maybe I can incorporate them at some point.
Thanks. A couple points to help you along.
1. You will note the welded on nuts on the receivers. I put one on the side and one below over new holes I drilled. That way I could take out the slop normally present in receivers with a 1/2" bolt with a welded on handle. I have found I really don't need the hitch pins as those T-handle screws hold things quite well. I suppose if I was pulling directly outward on something hard it might be good to have them in place, but I haven't run into the need at all. Photo of the T-handles below
2. The extensions mostly serve their purpose, but they are horribly not in plane with the main table. As such they are useful as support surface, but I cannot rely on them in any sense for keeping things flat or square. I'm not 100% sure what went wrong. There is some welding warpage for sure, But i suspect i approached it wrong in how I pulled it all together. I probably should have welded on the supports first, left them long and then milled or ground them down to make it all work right.
Northern has weld-on receivers for $15 and I see Amazon is about $12, so they aren't horribly expensive.
Lis - Yes that is the one, only with my new rollers.
Below is a shot of the mount I made for the vise which shows the detail a bit better. you can see a lot of shims under the table top if you look.
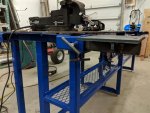